Windscreen de-icing system
Monday, 28th July, 2014
The process of fitting out the cockpit in the space below the waist longerons has to be completed at an early stage, because once the upper sidewalls are installed assess becomes difficult, if not impossible. I made a tentative start of the starboard lower sidewall last autumn with the completion of the windshield de-icing fluid tank (see my blog of December 2, 2013), and this is where I picked up the thread again some ten months later.
The arrangement of the de-icing system has the advantage of being very easy to interpret from photographs and GA drawings. It consists of a closely clustered group, which includes the tank, a pressurising pump and a control cock, all interconnected by copper pipes of varying diameters.
The tank is simplicity itself to build, comprising of a solid styrene block detailed with turned aluminium and brass parts. Less straightforward is the bracket and strap arrangement used to secure it the airframe. I made this from folded litho-plate parts, copying the full-size arrangement closely. However, rather than attach the tank to the fitted brackets, I built the brackets around the tank and drilled the back of it for a round plastic peg. This made installation a lot easier.
The de-icing control cock is mounted on a plate bolted to an intercostal between frames 9 and 10. What the eye can’t see behind it comprises of a small cube of styrene drilled at the bottom and both sides to support three turned hexagon brass pipe unions The plate itself is folded litho plate and it is detailed on the front with an aluminium disk embellished with tiny forward-aft stops for the tap and a big hexagon brass nut.
The control cock itself – a casting in the real aircraft – posed the only significant challenge because of its sculpted shape. This exemplifies how the model maker must mentally devolve tricky three-dimensional shapes into their more fundamental forms.
I began by cutting and drilling the side-view from aluminium sheet, and built up its cube-like body from two pieces of triangular-section styrene rod glued either side and capped with a tiny square (cut from 15 thou micro strip) to represent the steel shaft. The cylindrical front end, which engages against the stops, is impersonated by a piece of styrene tube slit down one side and slid onto the aluminium flat wit a dab of superglue. Seen in plan view the cock assumes a wedge-shape, and I developed this by using tiny amounts of plastic metal applied with a scalpel point and cut to shape with needle files.
Finally, after painting, I plugged the hole left at the top of the styrene tube with a tiny brass stud and locknut and drilled one flank of the square boss for a brass fixing screw. I photographed the finished assembly (which comprises of 23 individual parts) alongside a picture of the real thing, and I think it passes muster.
Building the brass pressurising pump and needle valve mainly involved lathe-work, with its ten or more components turned from hexagon stock and soft soldered together. Only the lower end of the barrel is glued in place, and that after the pump had been installed into its bracket on frame 10, where it is retained in place by three tiny screws.
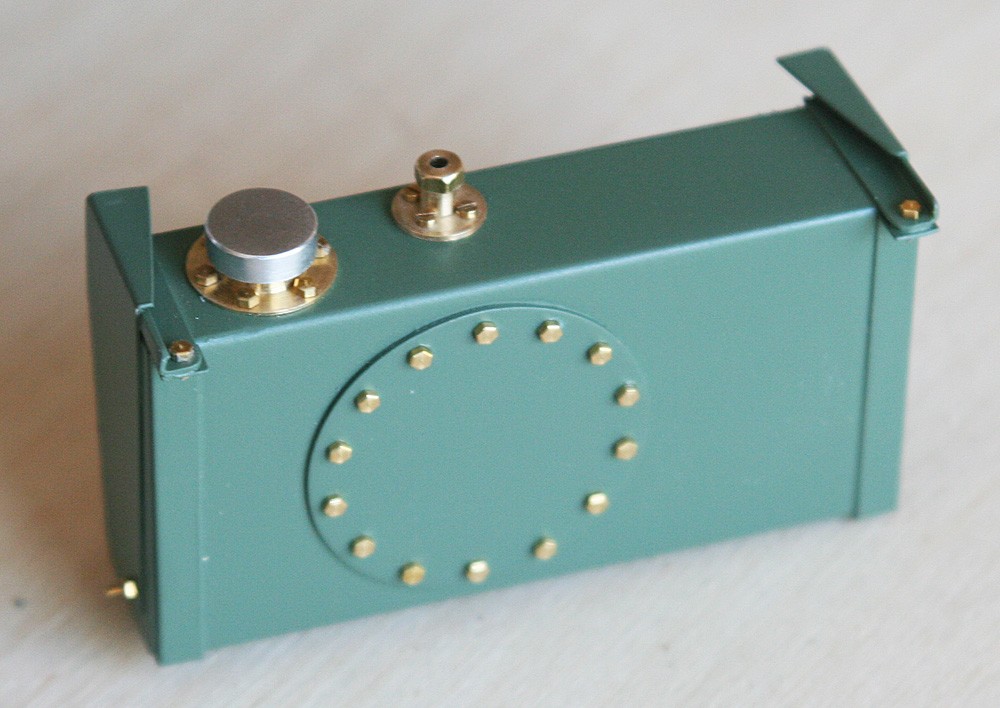
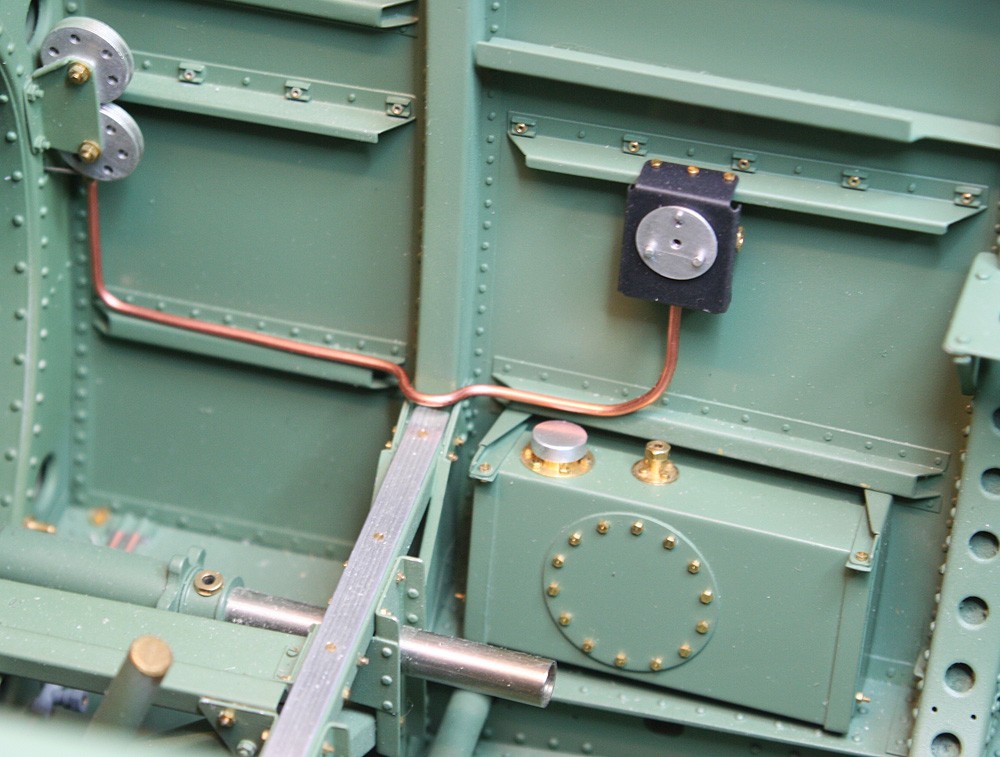
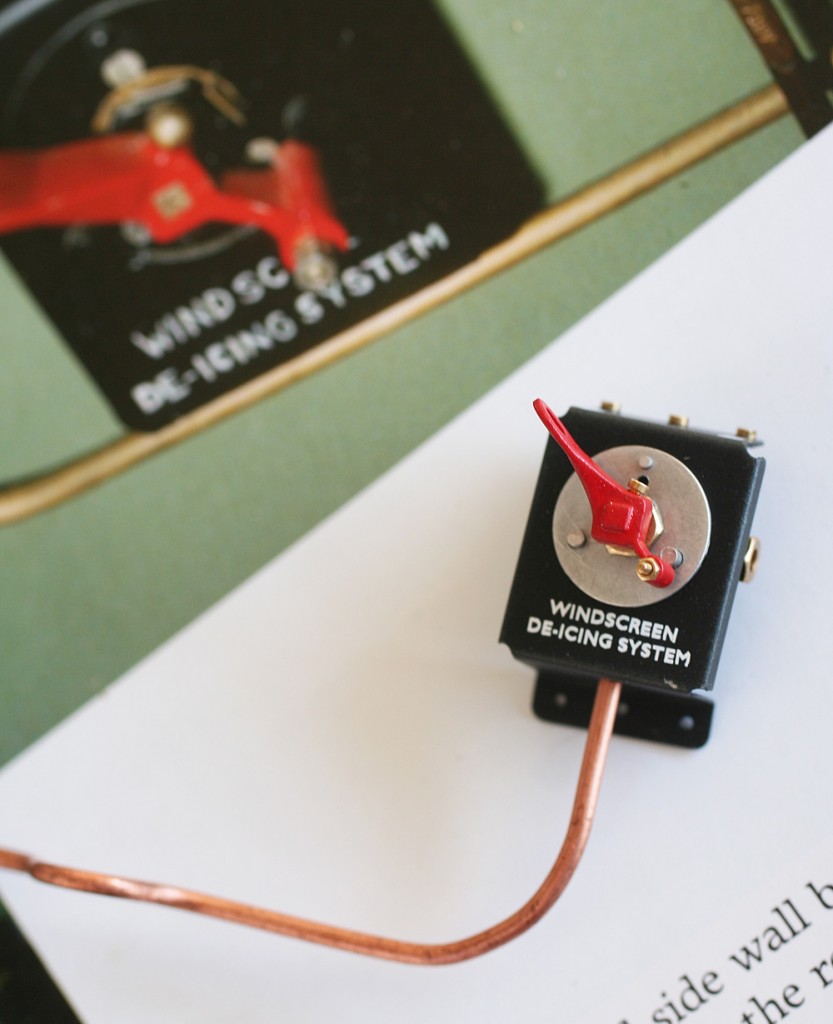
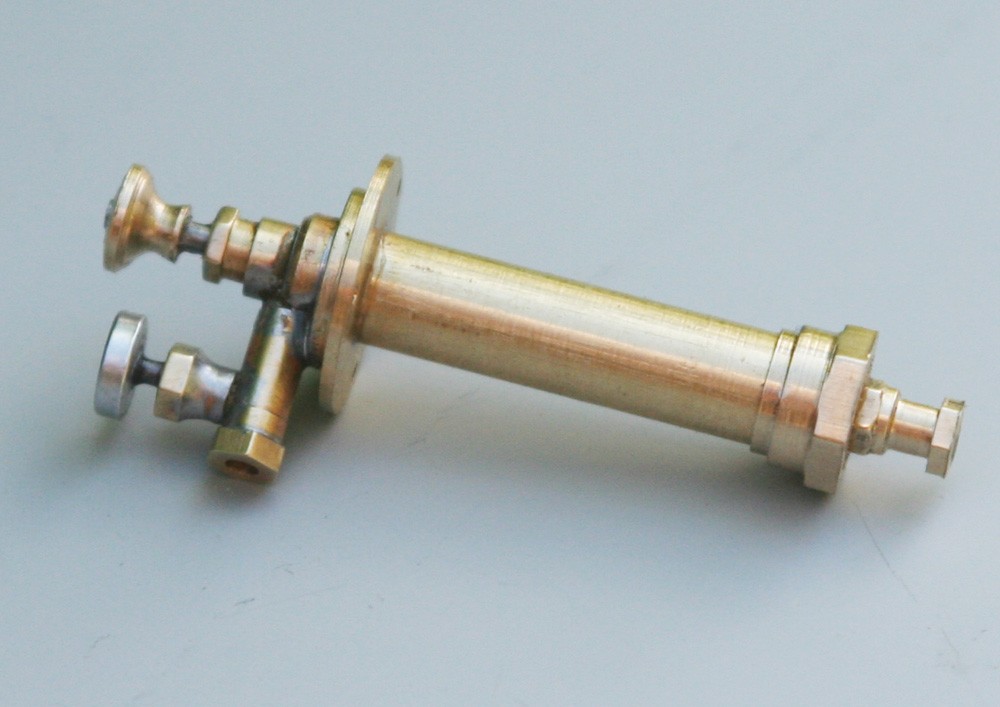