Filling gaps in the fuselage shell
Friday, 29th August, 2014
The detached but otherwise completed top half of fuselage frame 11 has been gathering dust in my workshop for almost a year, so its permanent installation marks a milestone in the model’s progress.
I described in my last two blogs the dual voltage regulator pack, pilot’s head armour and seat support structure. One further item needed at this stage is the highly visible top longeron extension that locks frames 11 and 12 along the dorsal midline. Fortunately, I discovered its V-shaped cross section illustrated in the Spitfire repair manual, which, in the absence of a better drawing, has enabled me to copy it using folded litho-plate as shown in the accompanying picture.
It is secured to the airframe by two pairs of angle brackets, and its spade-like forward end caps and juts slightly forward of frame 11, providing anchorage for the glazing arch and canopy locking plate. I made the latter from a scrap of sheet brass, folded into a z-shape (up-curving at the forward end) and pierced with a small rectangular hole.
It is crucial at this stage to make provision for the sliding canopy tracks, and informed by the dimensions of the recesses in the mainframes, I have used 5.5 x 3.5 mm brass channel section (of the sort available in hobby stores) as my starting point. The first job was a ‘dry fit’ trial using two ‘as supplied’ 12-in. lengths of ‘K & S Engineering’ brass to check for alignment over the entire span in both side and plan views. To my relief they pointed unerringly to the two marks I had made on the sides of frame 8. Satisfied, I cut two lengths to represent the rearmost portion of the rails aft of frame 11 and glued them into position, confident that I will be able to preserve the alignment when it comes to installing the remaining sections later.
Now, finally, I could add skin, starting at the gap behind frame 12. Mindful of the need to build in a sturdy foundation for the fixed canopy, I cut this section from two pieces of 0.5 mm sheet aluminium, curving them by hand to the exact fuselage contour. I added a single strip of 1.5 mm thick styrene to provide a crisp, clean edge where the glazing will abut, then filled the gap in the middle with 1/8 balsa cut so as to bend along the grain and left full for sanding back later.
Bonded by liberal applications of cyanoacrylate, the three-part laminate makes for a thin yet robust structure that will be reinforced in due course by the model’s exterior litho plate skin. The two shallow cheek pieces above the canopy rails, are built up in the same way – alloy sheet followed by styrene followed by balsa.
This left the two main skin panels between the rail and waist longeron, and I made and fitted these much along the lines of my diary entry of November 13 last year, so I’ll refrain from further elaboration here. It is worth mentioning, however, that because of the obvious practical constraints on using an airbrush safely within the fuselage most of the panels were primed and painted cockpit green before being fitted. It is not the ideal option, but with care it works.
If you have spotted an obvious weak spot you are correct: There is no landing provided for either above or below the newly installed canopy tracks; the skin panels simply abut the brass at top and bottom and are held there by their own rigidity and the grace of superglue. However, the tracks in their present state are mere shells. They closely approximate to the correct dimensions as viewed from behind, i.e. from within the fuselage, but they will need to be built up on the reverse side to match scale internal dimensions and section. This additional material will provide a small but significant overlap for the litho plate outer skin, which I am banking on to consolidate an otherwise weak spot in the fuselage shell.
To conclude this stage I made the arch-shaped fixed canopy frame from 5 x 2 mm rectangular brass section, filing off one of the narrow faces, so as to convert it to a deep channel section of approximately the correct dimensions to accommodate the glazing. I packed the aperture with a matching length of close fitting brass rod and heated the whole lot cherry red with a butane-torch, rendering the annealed metal easily formed to shape with the help of a sturdy internal template cut accurately from six-ply. The removable brass rod stops the channel section from pinching up during the bending process. Once shaped, the piece is matched centre line to centre line on the model, and the two descending arms marked and cut to exact length.
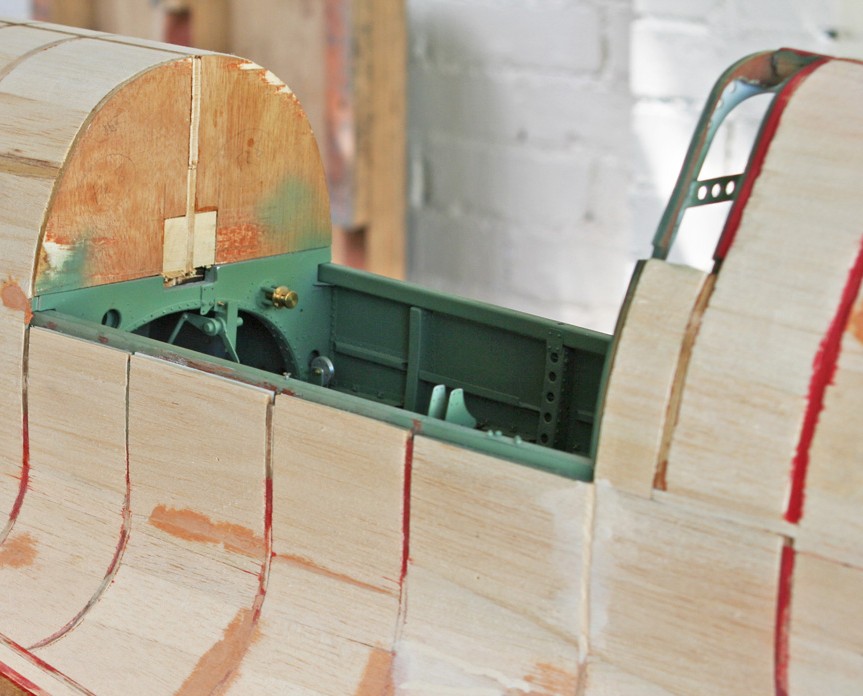
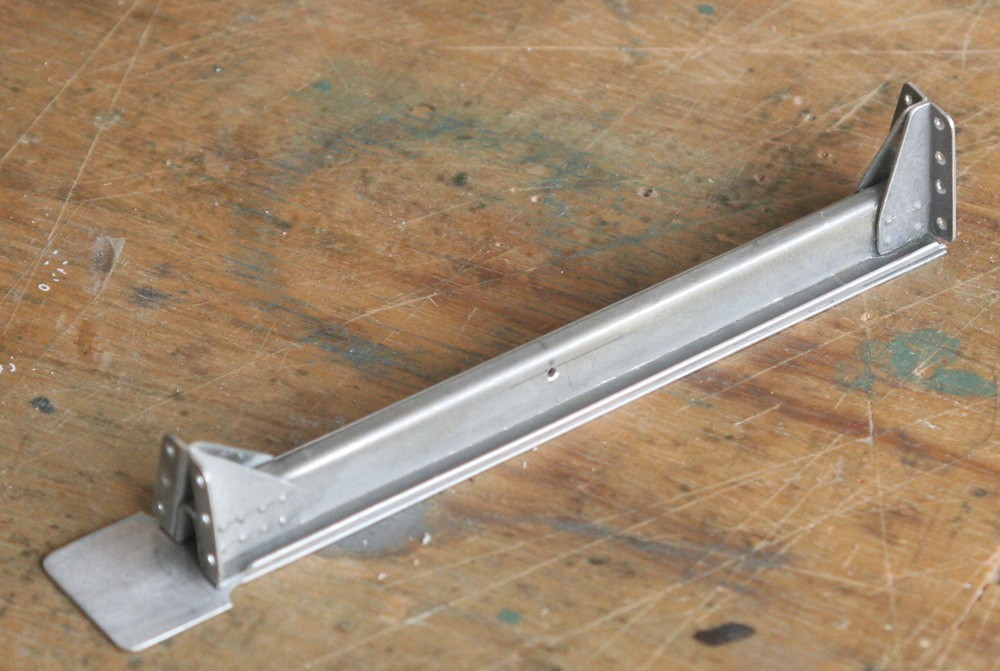
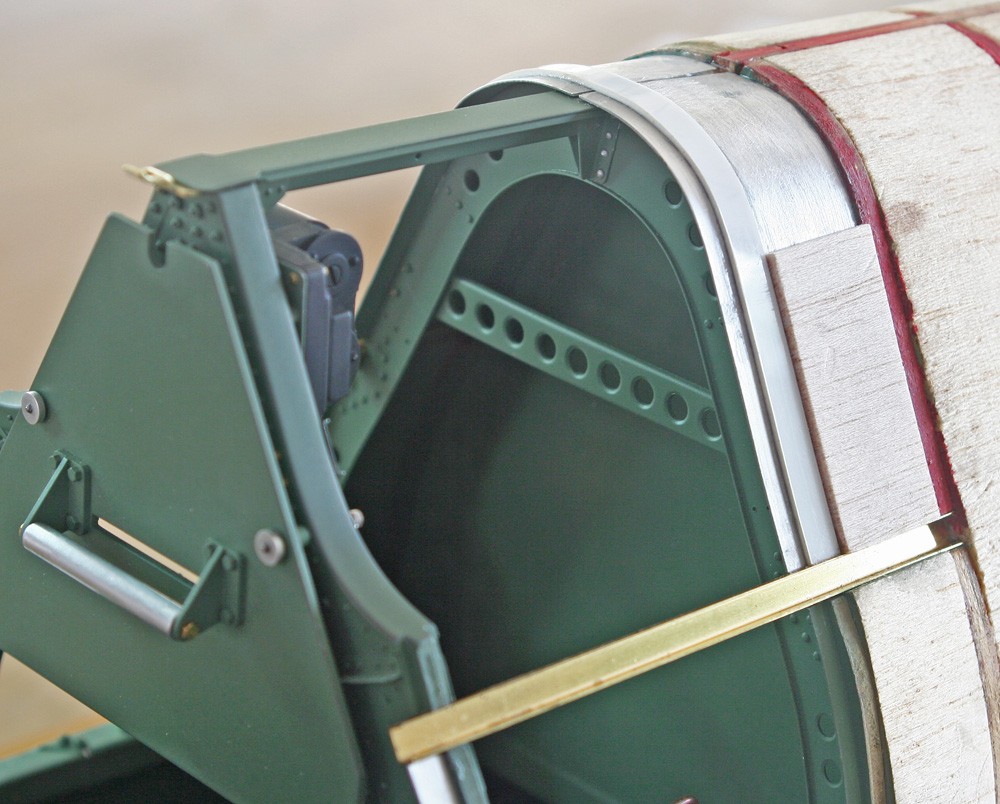
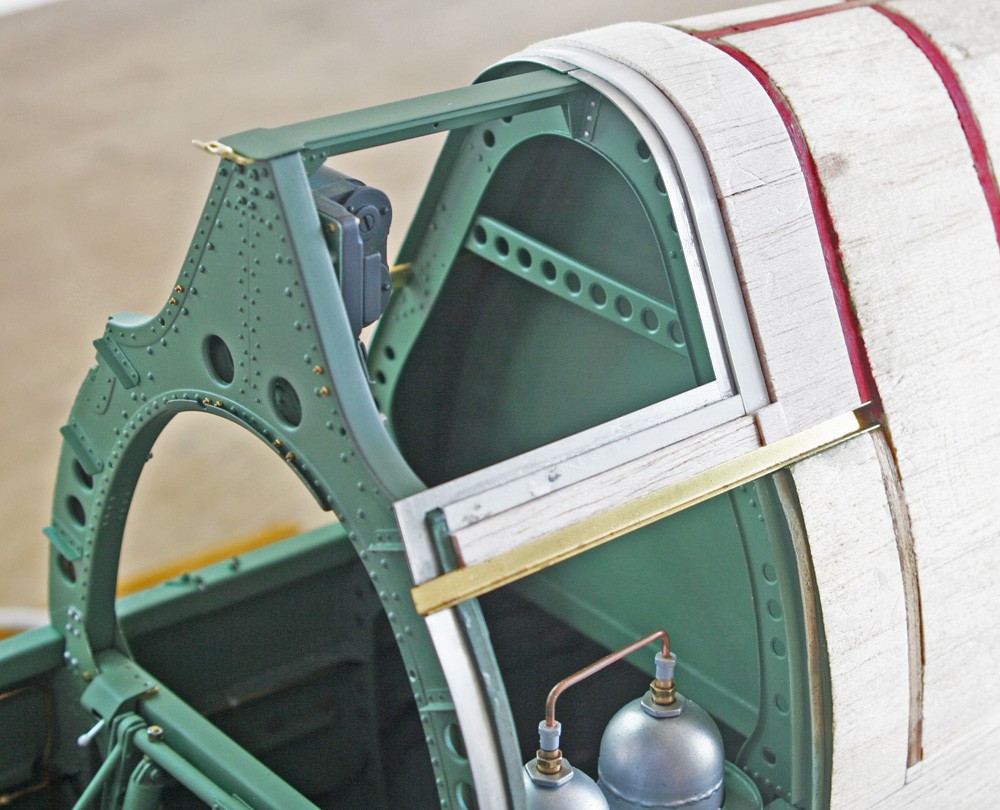
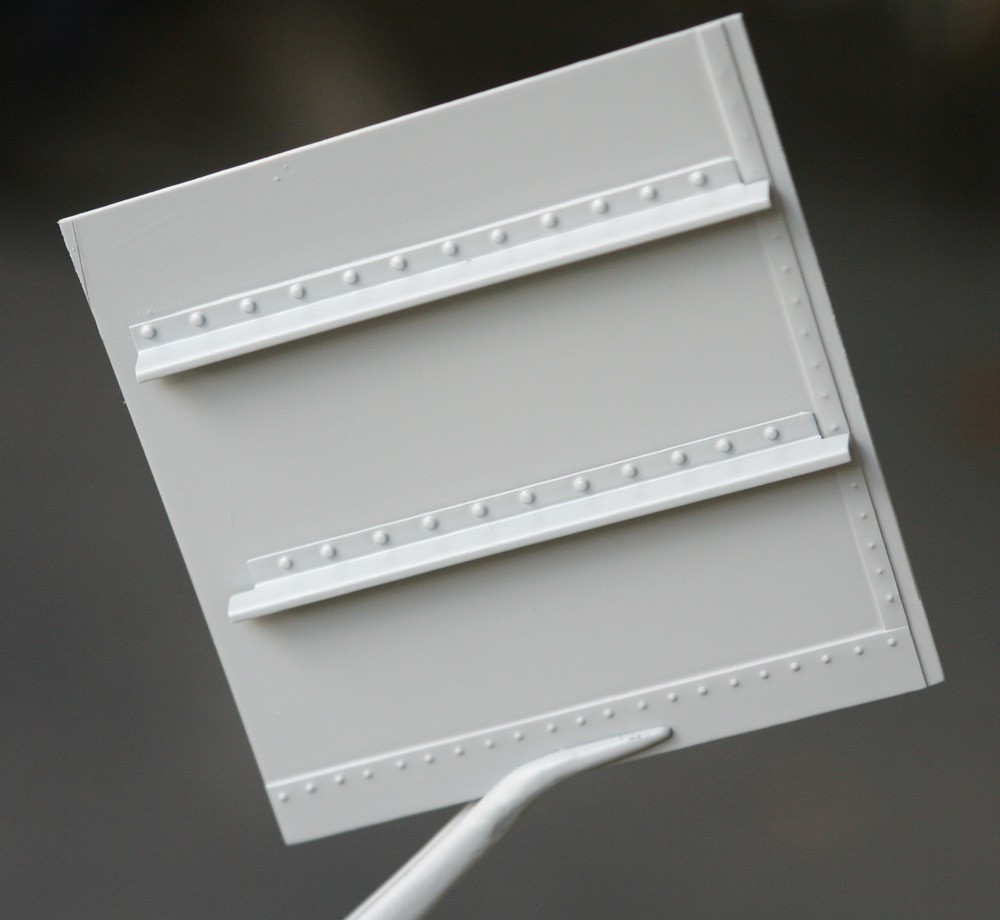
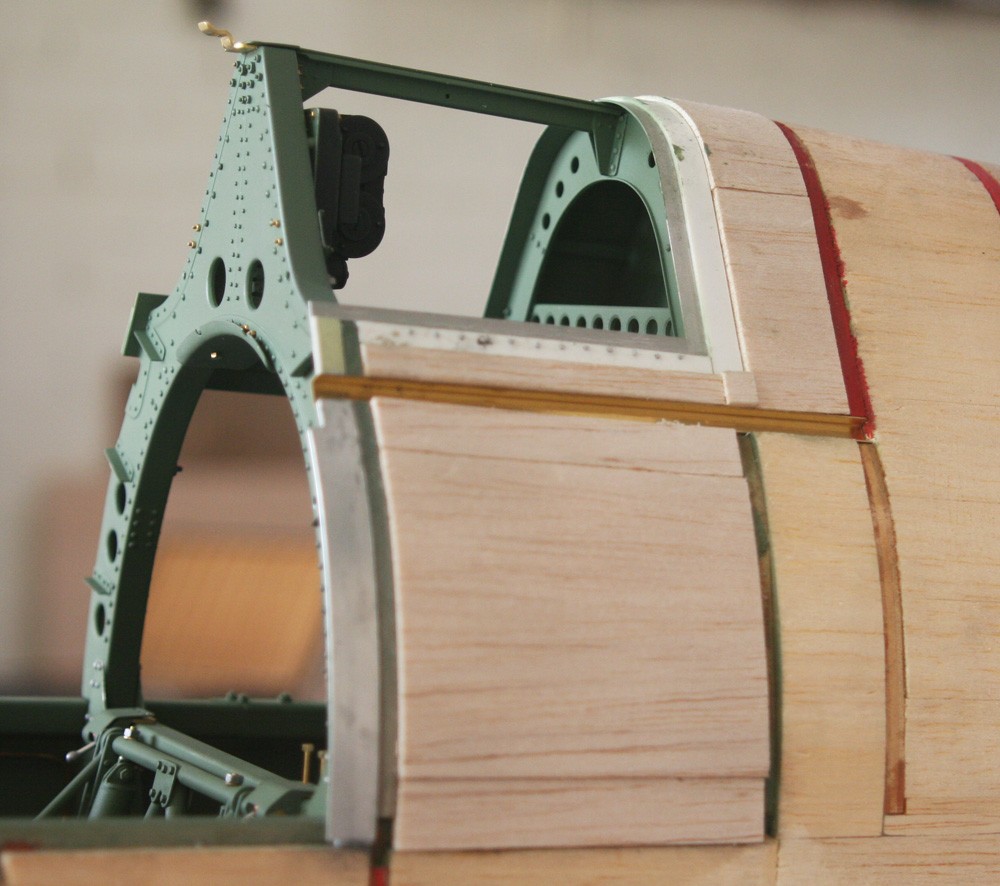
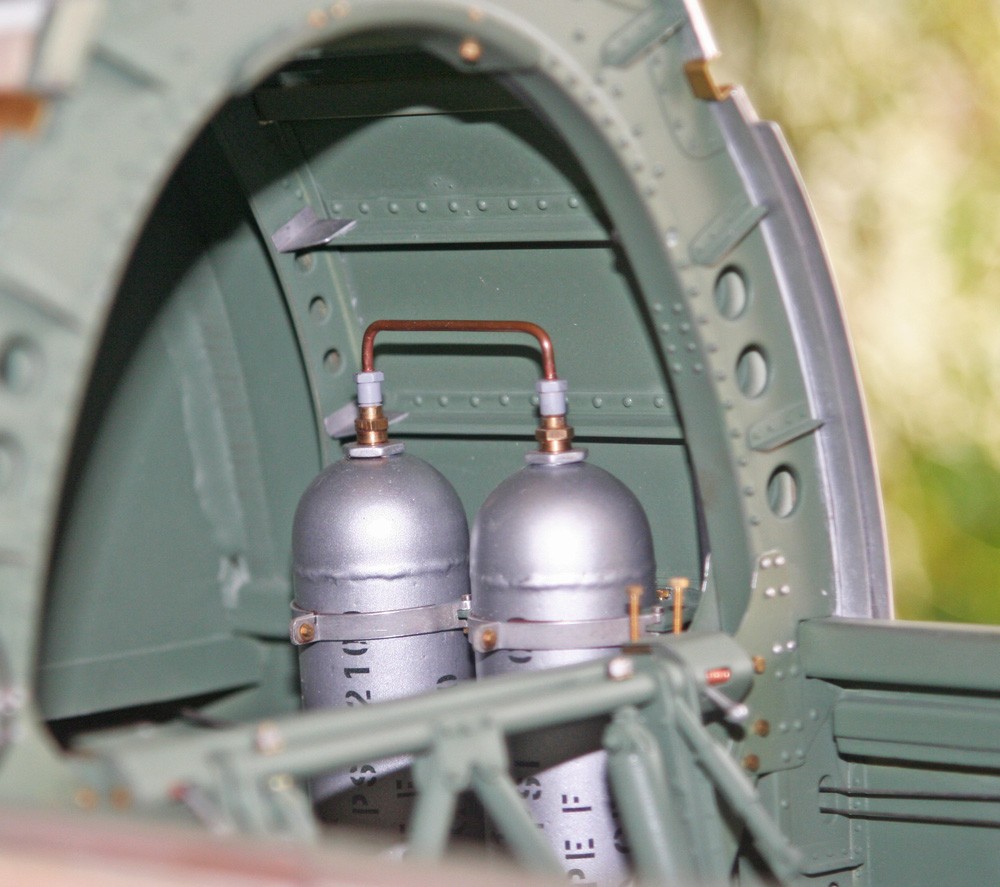
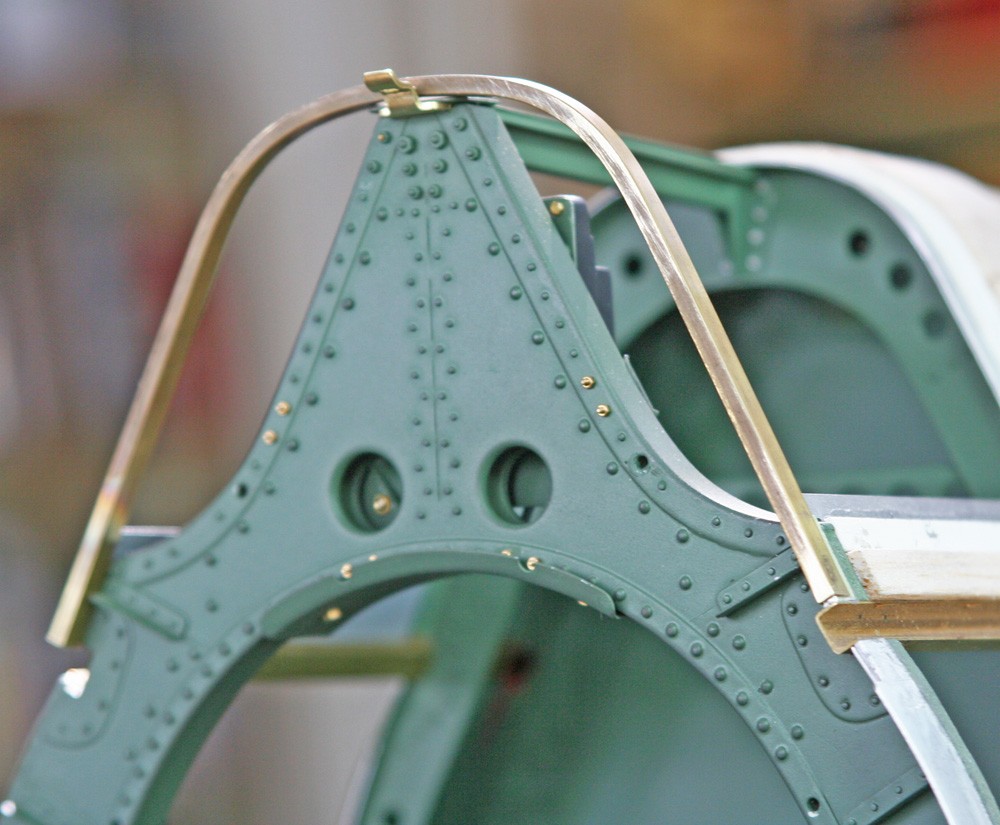