An experiment in panel beating
Wednesday, 30th December, 2015
I had long anticipated a major challenge when it came to the cowl panels. And as anticipated, I found it impossible to force litho plate – even when repeatedly annealed – to adopt the underlying lower cowl contours, even though it consists of port and starboard halves. Never in my two previous models had this happened, and it demanded a radical new approach if this third project was ever to see completion: I would have to become a panel beater!
I say in all sincerity that I entered into the experiment more in hope than with any real prospect of success. Hitherto my technique involved burnishing the softened metal from the outside, thereby forcing it down onto the wooden airframe (the pattern) until it assumed the underlying shape; now I proposed working from the inside of the panel, and mainly by an unpractised percussive process carried out remotely from the airframe!
My first step was to make a paper pattern so that I could cut my litho plate blank as closely to finished size as practicable. I procured a suitably sized pad of inch-thick balsa and sorted through junk until I came up with a small pine offcut that had once adorned a bedpost. With the litho plate carefully annealed, I placed it onto the balsa and began to tap away.
The first attempt took the best part of a morning of continuous tapping, rubbing and repeated annealing. To begin with the shape looked horrendous, but with patience and perseverance, and a sort of a sixth sense that model makers acquire, the desired shape began to emerge, and the more I developed a feel for the process so the more that shape evolved.
I learned to combine my tapping with a vigorous lateral rubbing motion, and that by exchanging the balsa for a much harder wood support I could remove localised inconsistencies. Then it became a matter of alternating between the two, while repeatedly offering the work-piece up to the model to check progress.
It was a long and uncertain process that involved a failure or two, but in the end it worked! I had actually beaten a panel of litho plate to near enough the shape of the lower cowling and then sufficiently refined its surface finish to be confident enough to glue it to my model reasonably certain that any minor inconsistencies remaining could be removed with abrasive paper and elbow grease.
Of course, two lower cowl panels are needed, so the process had to be repeated for the port side, but this time with the secondary challenge of obtaining an accurate abutted panel seam down the mid-line of the nose. Here my technique is crude, yet it works: I simply dress the extreme edge of the installed panel with enamel paint. Then the oversize matching panel is positioned exactly and carefully lowered down, such that the thick wet paint imprints onto its under-surface. The line is not always perfect but more often than not sufficient to work to.
Trimming annealed litho plate requires extreme care, and I find sharp scissors the best tool. As anyone who is familiar with my work will know, my skin panels are invariably glued to the airframe using contact adhesive.
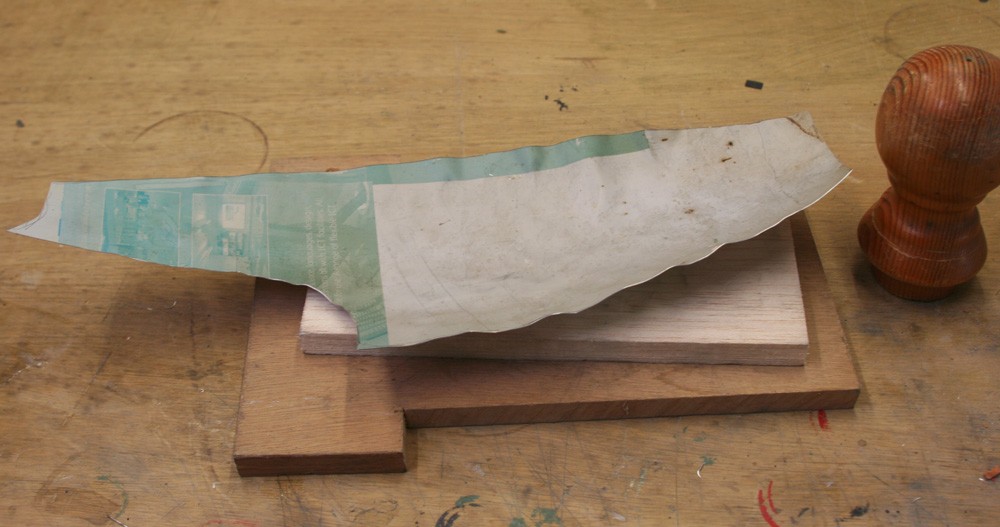
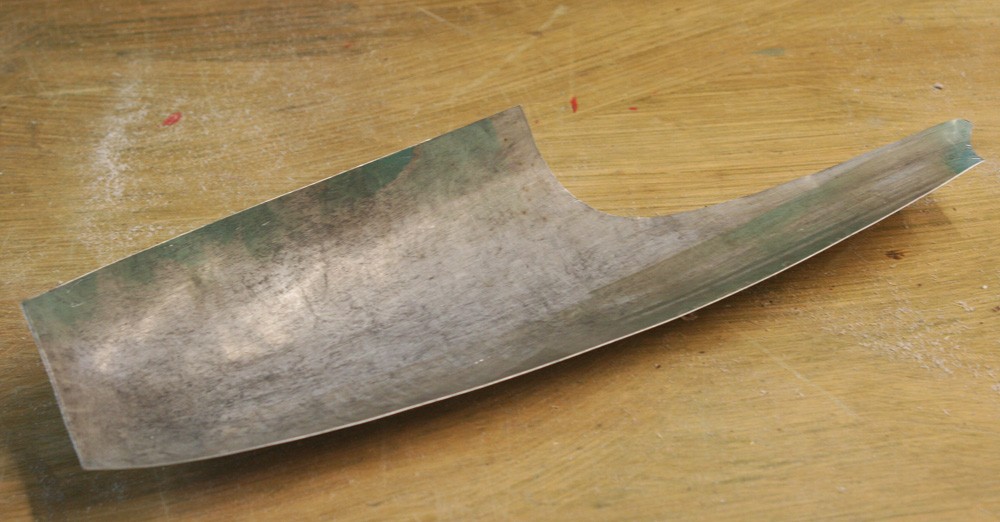
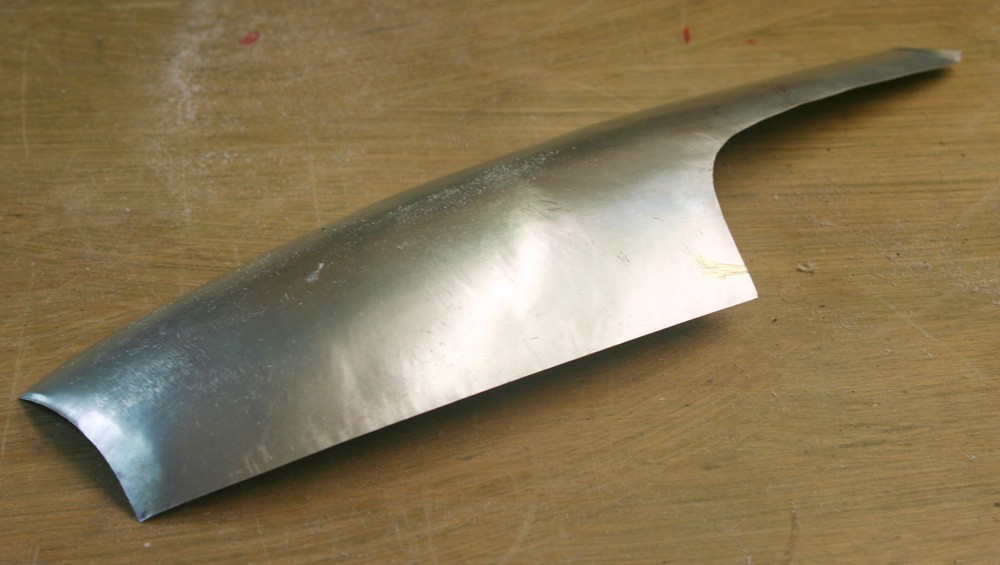
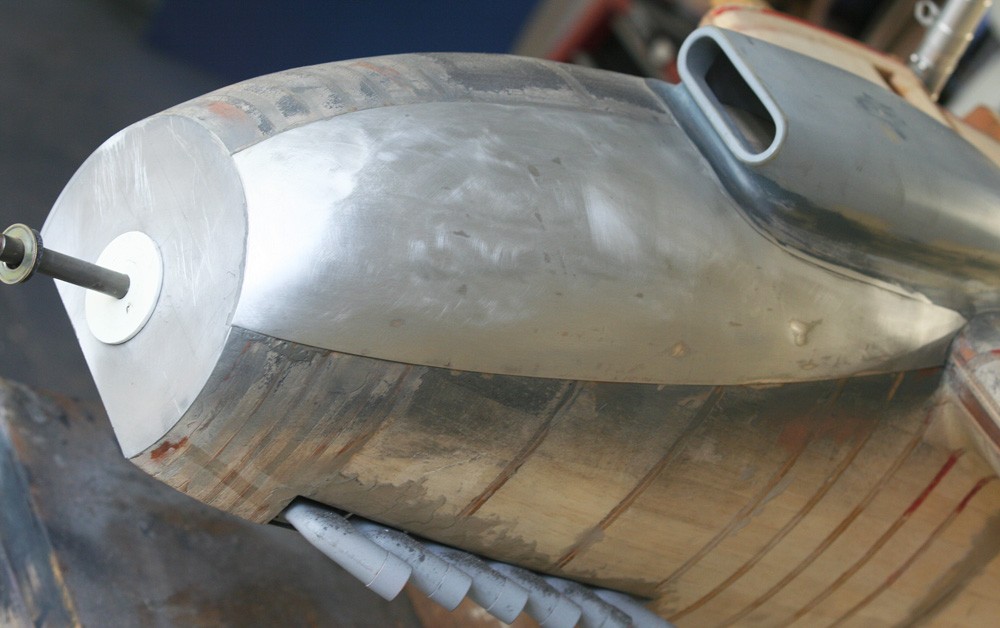
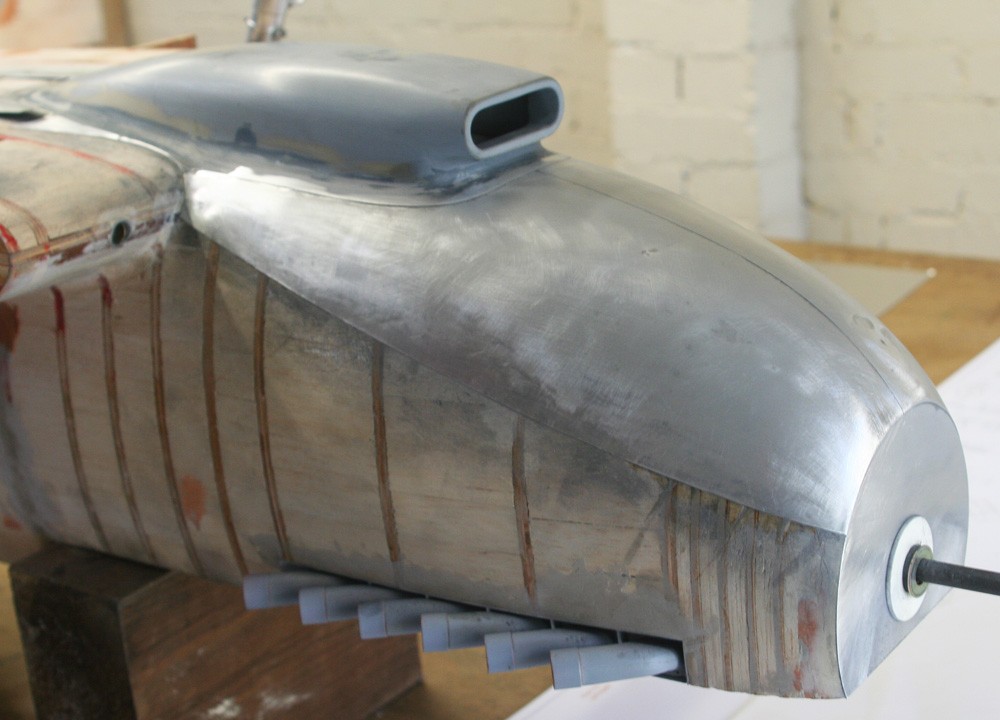